Since the explosion in the port of Beirut in 2020, the world has become more aware of the dangers of ammonia. Not only ammonia, but also hydrogen and methanol, are key elements in the energy transition, but also have hazard potential. Handling these substances requires specialist knowledge and a strong focus on safety. Fortunately, the industry has the necessary experience.
Building on decades of experience in the safe management of highly flammable, explosive, and toxic materials – including hydrogen, ammonia, and methanol – the industry is well-placed to handle increasing volumes of the substances as their production, use and transport will increase to meet defossilisation goals. The priority now is to produce them sustainably, using renewable electricity for green hydrogen. At the same time, safety standards for storage, transport, and use must be further improved.
Understanding the risks of hydrogen
Hydrogen is the most abundant element in the universe, yet its reputation is one of a particularly dangerous substance. What is often overlooked is that hydrogen is not inherently more dangerous than any other energy carriers – the risks lie in the details of its handling and its specific properties. In the same way that we handle highly flammable substances such as propane or liquefied gas on a daily basis, hydrogen also requires precise safety measures. Hydrogen has been known in the industry for over 200 years and is used in a wide range of sectors [1]. The handling of hydrogen is by no means a new issue – the technology and safety standards have been continuously improved and developed over decades.
To realistically assess the risks associated with hydrogen, it is first important to understand its physical properties. Hydrogen is characterised by:
- Lightness: Hydrogen has a very low density and rises quickly when released. Unlike other gases, which can spread throughout a room, hydrogen dissipates rapidly into the atmosphere. This reduces the risk of forming an explosive mixture with air in an open or well ventilated space. However, in confined or poorly ventilated areas, good ventilation must be ensured to minimise the risk.
- Odorless and colorless: These properties not only make it difficult to detect leaks, but also to recognise a hydrogen flame (Figure 1), as it is also invisible and emits very little heat. Precise monitoring of hydrogen systems is therefore essential. However, modern sensors and detection systems are capable of detecting leaks at an early stage, significantly minimising the risks.
- Liquid hydrogen: At extremely low temperatures (below -252.8°C) hydrogen becomes liquid. In this state there are additional hazards due to the extreme cold, such as hypothermia or frostbite on skin contact. However, these risks can be effectively mitigated by appropriate safety measures, such as special protective clothing and precise control systems.
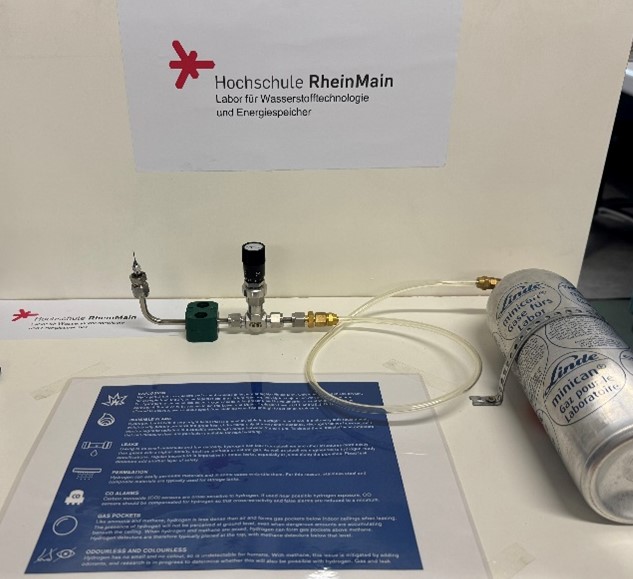
The regulations governing the storage, transport, and use of hydrogen are well established and have evolved over many years. The infrastructure used in industries such as chemicals, food production, and energy is specifically designed to meet the requirements and mitigate the hazards associated with the gas.
The potential hazards of hydrogen, such as explosions, are the result of improper handling, inadequate safety measures, or technological failures [2]. However, these risks are not unique to hydrogen. Similar hazards can occur with other fuels, such as natural gas or LPG, if safety protocols are not followed. This means that the risks associated with hydrogen are not inherently higher — they just need to be carefully monitored and controlled like any other fuel.
The familiar substance ammonia
Ammonia is a key component of many industrial processes, particularly in fertiliser production, but also in refrigeration and the chemical industry. Although ammonia, like hydrogen, is toxic and hazardous, the industry has decades of experience and knowledge in the safe handling of ammonia [3]. With proper safety measures and a thorough understanding of its chemical properties, the risks associated with ammonia can be significantly reduced.
Ammonia is highly reactive, especially in acid-base reactions. It is toxic and poses significant health risks. These properties require strict safety precautions, which is why ammonia has been extensively studied over a long period of time, and the industry has developed a comprehensive body of safety knowledge that continues to evolve.
To better understand the potential hazards of ammonia, it is essential to examine its physical properties:
- Density and dispersion: Ammonia is a highly volatile gas that dissipates rapidly when released. This reduces the risk of dangerous build-up in open areas. However, in confined or poorly ventilated spaces, ammonia can accumulate rapidly and pose a health risk, so special ventilation and exhaust systems are essential.
- Toxicity: Ammonia is toxic even at low concentrations and can cause respiratory, eye and skin irritation. At higher concentrations, the risks increase significantly and can lead to serious health problems or even death. Therefore, protective equipment and adherence to safety protocols are essential to protect both people and the environment.
- Storage and transport: Ammonia is stored in large quantities as a liquid gas in industrial applications [4]. This places high demands on the safety of storage and transport systems, which are designed to prevent leaks and accidents. The use of special pressure vessels and cooling systems is essential for the safe handling of this substance.
The hazards of ammonia should not be underestimated. Its toxicity and potential environmental risks are serious concerns, but they can be largely controlled with appropriate safety measures. The industry has decades of experience in the safe handling of ammonia, particularly in fertiliser production and refrigeration. By strictly following safety guidelines and using advanced detection systems to monitor for leaks and releases, potentially hazardous situations can be identified and mitigated early.
Due to the high toxicity of ammonia, it is essential that companies to follow strict safety protocols. These include regular maintenance of equipment, comprehensive training of personnel, and the implementation of emergency response protocols. Such preventive measures help to ensure that the risk of accidents and health hazards remains low.
Widely used methanol
Methanol has a long history in the chemical and energy industries. It is used in many industrial processes, including fuel production, the solvent industry, and as a raw material for many chemicals. Methanol is classified as a hazardous substance, but with the right safety precautions, the risks can be effectively managed [5]. Methanol is a volatile, highly flammable substance that is combustible in its liquid form. Despite these properties, the industry has long experience in the safe handling of methanol and has developed numerous technologies and safety measures to minimise the risks.
To realistically assess the risks associated with methanol, it is important to understand its physical properties:
- Flammability: Methanol has a low boiling point and is highly flammable. However, as long as established storage and handling protocols are followed, this does not pose an undue risk. These protocols have been in place in the chemical industry for decades.
- Toxicity: Methanol is toxic in higher concentrations and can cause serious health problems, including fatal poisoning, if mishandled. However, by following safety procedures such as using personal protective equipment (PPE) and ensuring proper ventilation, the risks can be significantly reduced.
Methanol is a flammable, toxic substance that poses a health risk if handled improperly. Compared to other flammable liquids, such as petrol or diesel, handling methanol also requires special care to avoid hazards.
Safety measures, such as explosion protection and fire prevention systems, make handling methanol safe to handle in various applications. Safety standards for methanol are well established in the industry, from the automotive sector to chemical companies.
Safety as the foundation for successful Power-to-X projects
The safe handling and responsible management of hydrogen, ammonia, and methanol is essential to realise the potential of Power-to-X (PtX) technologies. The properties of these substances – whether it is the high flammability of hydrogen, the toxic risk of ammonia, or the fire hazard of methanol – do indeed present specific risks. However, these risks can be controlled with the right technology, strategic safety measures and a proactive safety culture.
To ensure the success and scalability of PtX projects, the following actions must take place:
- Training of personnel
- Comprehensive risk assessments
- Fostering a safety-first mindset
- Adherence to industry standards
- Rigorous safety protocols
- Advanced monitoring systems
- Leak detection
- Proper storage solutions
- Collaboration across the energy, industrial, and regulatory sectors to develop a robust regulatory framework
- Sharing best practices for safety
- Continuous reassessment
- And many more
Sources
[1] International Energy Association (IEA) (2019), The Future of Hydrogen – Seizing today’s opportunities
[2] European Commission, Joint Research Centre (JRC) (2023): HIAD 2.1. European Commission, Joint Research Centre (JRC) [Dataset] PID: http://data.europa.eu/89h/1d6b06e9-3a89-4ec2-b051-3fb8a28eab9f
[3] V. Pattabathula, J. Richardson, American Institute of Chemical Engineers (AIChE) (2016), Introduction to Ammonia Production
[4] V. Pattabathula, R. Nayak, D. Timbres (2024), Ammonia Storage Tanks
[5] John V. Ashurst; Thomas M. Nappe (2023), National Library of Medicine, Methanol Toxicity
[5] Jaeger, P., & Salgado, T. (2023). Desalinización de Agua de Mar y Reutalización de Aguas de Desecho para la Producción de Hidrógeno Verde y Derivados en Chile. International PtX Hub